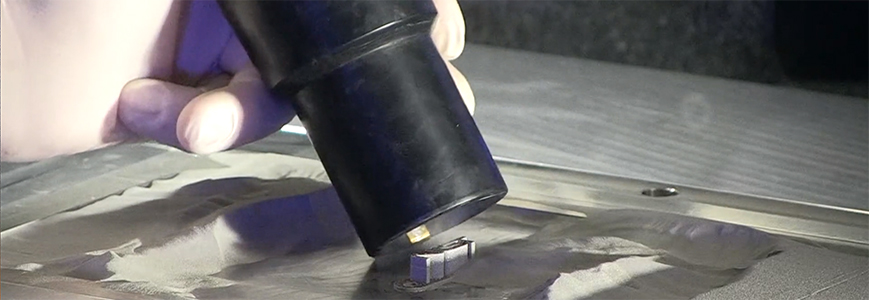
Credit: NIST
What's going on in that printing machine?
For surgical repairs to a patient’s hip or skull, surgeons might use a titanium bone implant. However, metal objects such as these – with complex outer forms, or with intricate internal features such as ducts or channels – can be difficult to make using conventional processes. To create these useful devices, manufacturers are turning to 3D printing, a process that typically involves building a part layer by layer, sometimes over minutes or hours.
3D printing of metal objects is a booming industry, with the market for products and services worth more than an estimated $2.3 billion in 2015 – a nearly five-fold growth since 2010. It’s increasingly popular in the medical, aerospace, and automotive industries, where it can be used to make complex components such as fuel injector nozzles for engines.
But the commercial technology is still relatively new, and maintaining quality control can be challenging and time-consuming. Two supposedly identical products made in the same way on the same machine don’t necessarily come out with the same dimensions. Tiny imperfections can appear in the layers, reducing the strength properties of the components. And residual stresses can build up as the layers cool, creating cracks between layers and warping the parts. The stress can be so high, in fact, that it can warp a 1-inch thick piece of steel by a millimeter.
To give manufacturers more control over this process, NIST researchers have built a metal 3D printing testbed, a custom-made printer that they can use to produce tools that will allow users to monitor the process in real time.
The researchers hope to answer some fundamental questions, such as: How hot does the melting metal get in each layer? How do you lower the stresses that cause cracking and warping? And what sensors would you need in order to provide better information about what’s happening inside the printing machine?
Eventually, the researchers hope their system will be useful beyond 3D printing of metal objects, to look at solid materials that experience extreme heat, such as the wingtips of supersonic aircraft.
No comments:
Post a Comment